Federico Baruffi is an Early Stage Researcher of the European project MICROMAN and PhD student at DTU Mechanical Engineering working under the supervision of Associate Professor Guido Tosello and Researcher Matteo Calaon. The industrial partner of his project is Ortofon A/S, a world leader in cartridge manufacturing and precision engineering.
His research topic is micro injection moulding, a manufacturing process used to produce micro plastic components, which are very common in the medicinal, communication, biotechnology, automotive and avionics sectors.
“The training I receive during the MICROMAN workshops is essential for the development of my project”, says the PhD student, “Learning from the leading experts in micro manufacturing and brainstorming with my fellow ESRs give me the tools for carrying out a fruitful research”.
In particular, the researcher at DTU investigates how to improve the quality control of micro moulded parts and, at the same time, make it faster and more efficient by decreasing the time-consuming measuring procedures that are applied nowadays in the industry. In fact, the current industrial state-of-the-art does not include a robust method to control the dimensional quality of micro moulded parts in-line, that is, during the very manufacturing procedure.
In a recent paper published in 2018 (available in open access here) Federico and his research team have proposed a novel way to assess the quality of a micro medical component in-line. In particular, they correlate the monitored process variables with the most important characteristics of the part, thus establishing a comprehensive strategy to verify the quality of each produced micro part right during the manufacturing process. “Such an approach can be the key for the next era of manufacturing”, adds Federico Baruffi, “Industry 4.0 will allow having an infinitely greater amount of data during the process, and this data must be used for controlling micro manufacturing processes aiming at zero-defect productions”.
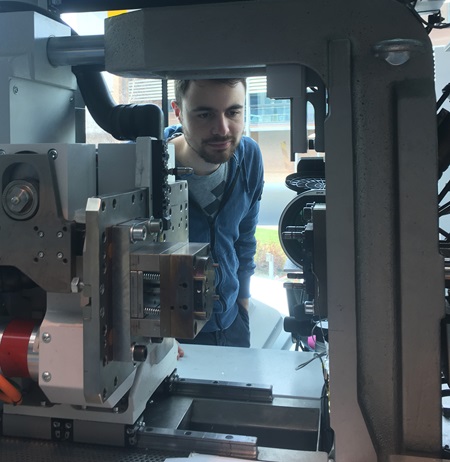
Federico working with the Wittmann Battenfeld MicroPower 15 micro injection moulding machine used in his experiments.